3m Multi-touchpoint Design Strategy
Skills
Journey Mapping
Multi-Touchpoint Design Strategy
Rapid Prototyping
Regulatory Constraints
Summary
3M Safety and Graphics asked us to review connected experience and journey map for a user of their hearing conservation product family, develop improvements to the product. We combined the felt needs of a Safety Manager with secondary research that revealed worker’s pain points and the regulatory constraints. This revealed strategic opportunities for product improvements. We then developed new applications of existing technology for this problem space.
Problem Analysis
3M’s user research group came to us with a research report of a user group of one of their product lines. The research detailed the emotional journey of safety managers along the touchpoints of hearing conservation device use on their teams. This research showed that the lowest points for safety managers in the process was in helping workers choose hearing protection type, testing for hearing loss and generating reports to show regulatory compliance.
According to the CDC, 22 million workers in the US are exposed to hazardous noise each year. According to a report of the 2011 OSHA Stakeholders meeting on Preventing Occupational Hearing loss, when given hearing protection, workers often did not use it on the job, despite knowing that it would lead to permanent hearing loss. We knew understanding why a worker would make a decision like this, and designing for that would get at the heart of the issue.
The reasons most workers gave for this were that hearing protection on the job site prevents them from communicating with their team, and that the devices they were given were not comfortable, or did not properly protect their ears.
Proposed Solution
Because of these factors our team set out to design a solution based around the industrial worker’s pain points. The goal of our work was to help workers feel empowered and equipped so that they are able to prevent hearing loss by focusing on convenience and personalization.
We designed to help workers feel empowered by giving them a choice of hearing protection devices, ranging from custom molded in ear protection system to an enhanced over the ear earmuffs that could be worn with a helmet or independently. This choice allows each worker to choose protection that is personalized and comfortable to them.
We designed to help workers feel equipped for the task of protecting their ears by ingraining hearing protection in the nature of their work and by providing a means to safely communicate with their teams while protecting their ears.
These new devices live at the job site and are safely stored and charged in secure and sanitary modules designated to each worker on site. The device storage point is unlocked and opened when a worker clocks in at the beginning of their shift. They are also required to be returned and charging when a worker clocks out at the end of their shift. When this happens, each worker is sent an end of day survey which prompts them to report and comment on their satisfaction with the device. This data is reported to the safety manager so that any issues can be addressed before permanent hearing damage occurs.
Each product line is designed to have an internal microphone which gives workers and safety managers feedback about the fitment of their device as they enter the job site. This feature is intended to provide workers with assurance that their hearing is protected and give managers reliable data about how well the devices are performing, and which workers are in compliance with regulations. They also have an external microphone which equips workers to talk to one another without removing their hearing protection by filtering out damaging noise and allowing spoken words to be heard.
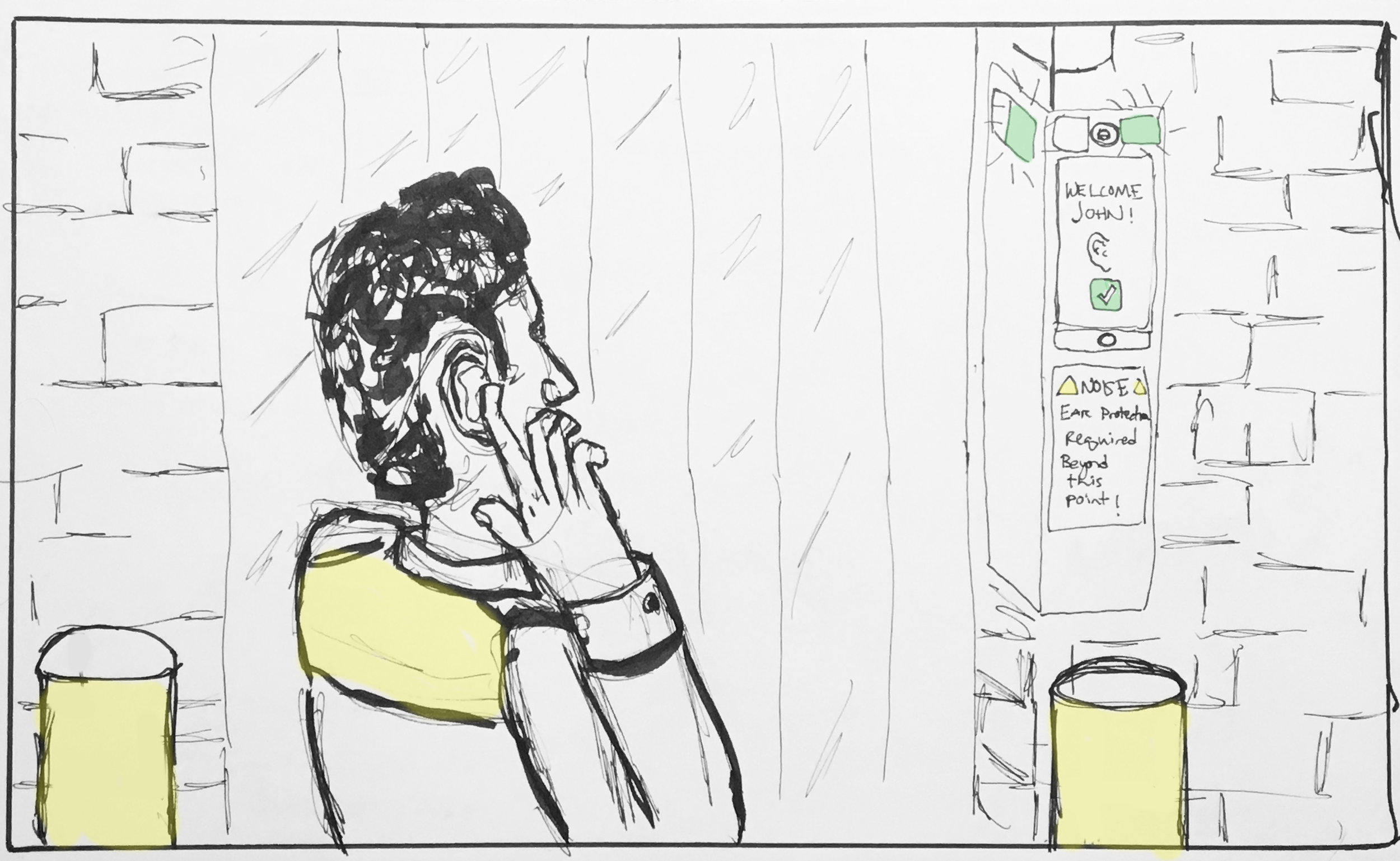
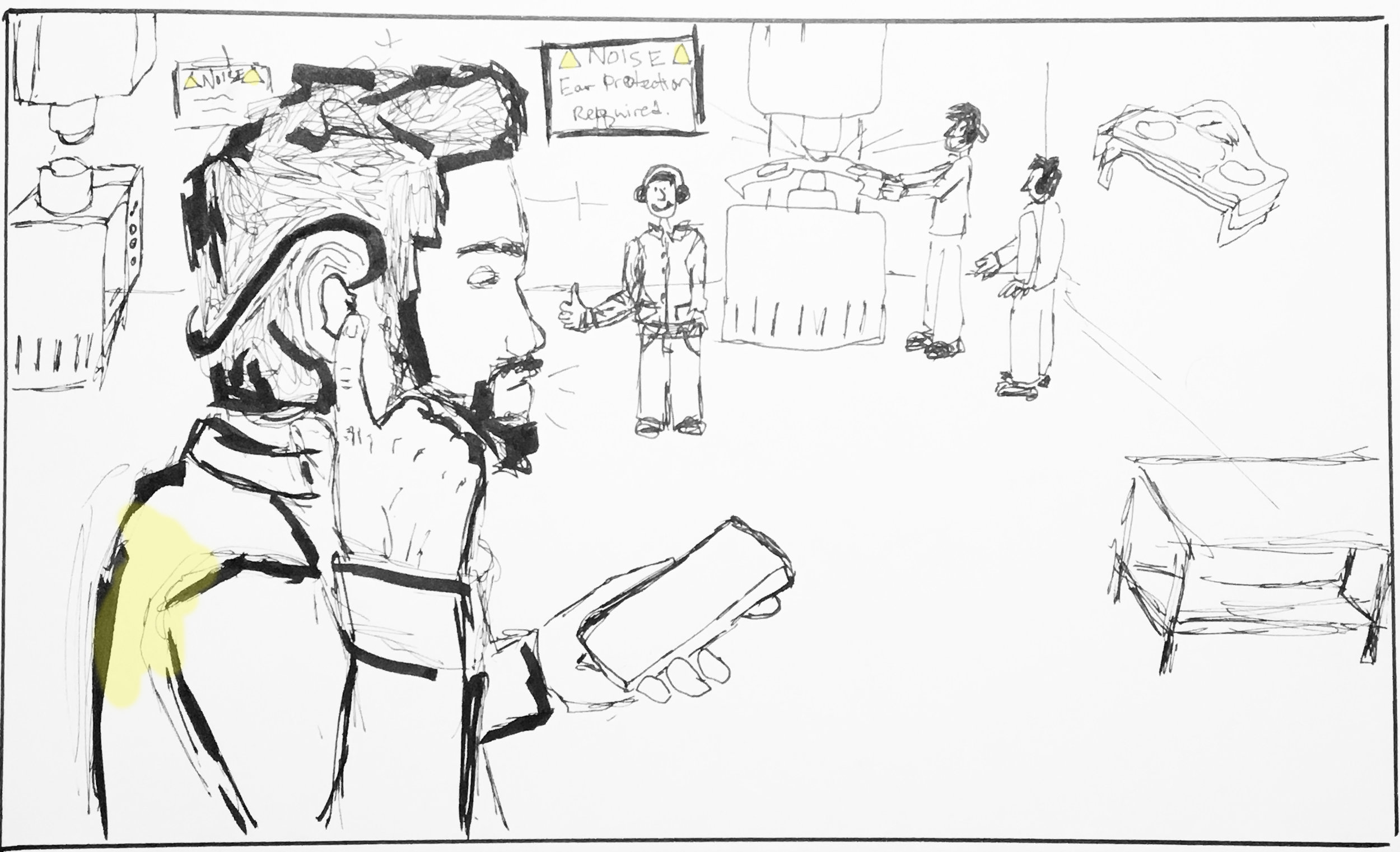
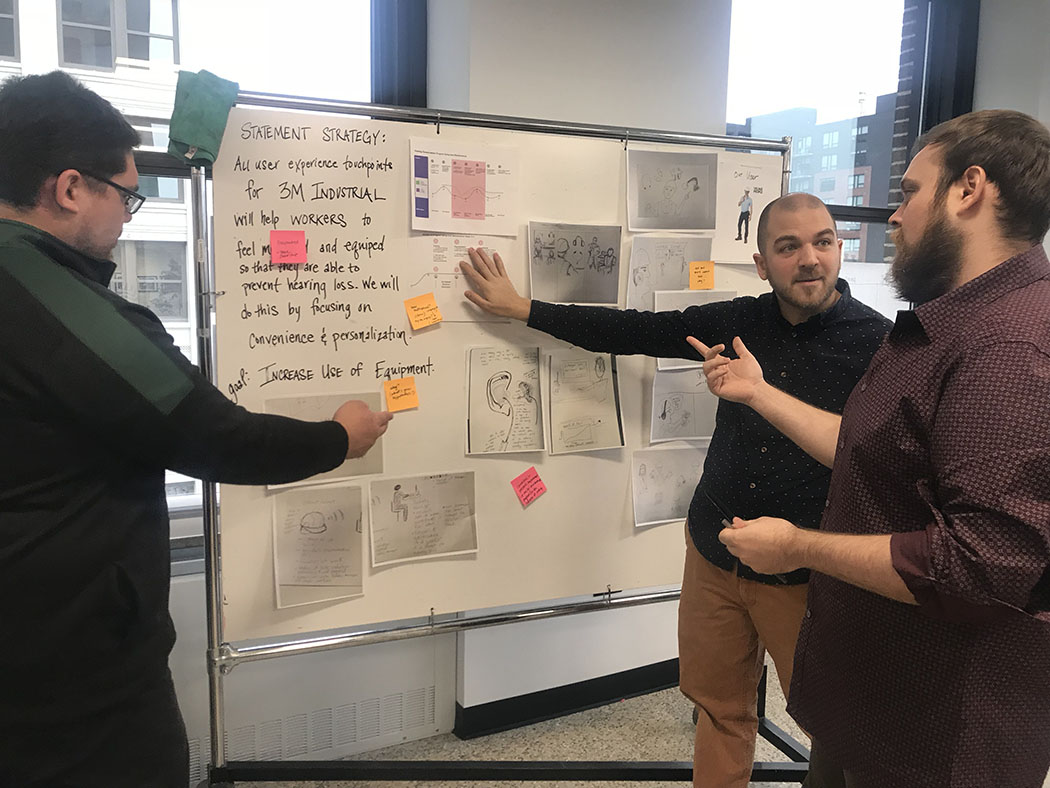
By designing around the end user’s pain points, and providing feedback to the safety manager we worked to ensure empowerment of the workers and raised the safety manager’s pain points as well. I noticed that in the user journey provided by 3M education of the worker came after several pain points. By rearranging the elements so that training comes first we were able to set better expectations for the workers and make the safety manager’s job easier.
Next Steps
We anticipate the result of these designs to increase the worker’s emotional state regarding hearing protection, while also increasing compliance and the safety manager’s ability to help their employees and report compliance accurately. We hope to further develop the technology needed to create custom in-ear hearing protection devices for same day, on-site creation.
Click here to download the design strategy implementation guide.